AI-Powered Solutions for Manufacturing
Industry
Transforming industrial operations with intelligent AI
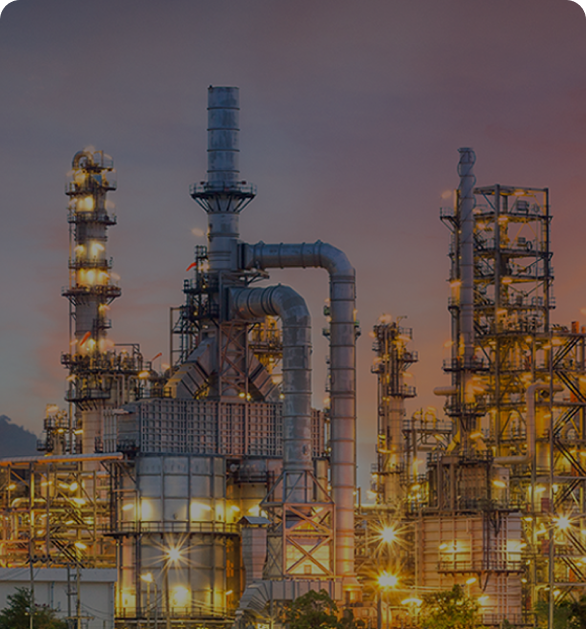
AI forecasts equipment failures, reducing downtime and repair costs by identifying issues before they impact operations
AI improves demand forecasting, inventory management, and logistics, ensuring smoother and more efficient supply chain operations
Computer vision identifies defects in real-time, enhancing product quality while minimizing waste and rework in manufacturing processes
AI monitors and optimizes energy usage, helping industries cut costs and lower environmental impact through efficient energy management
Integrated digital solutions company with expertise in IIoT, cloud, computer vision, and AI/ML use cases
Adept at implementing industry best practices and developing solutions to drive digital transformation
Offer predictive maintenance, asset monitoring, and energy efficiency to leaders in various industry verticals
Powerful alliances with hyperscalers and software leaders who build effective, futuristic solutions
Enhance exploration efficiency, reduce costs, and improve mineral quality using AI, vision technology, and ethical mining practices
Automate manual tasks, optimize metals balancing, and integrate production systems with accounting to improve efficiency and accuracy
Analyze data to predict equipment failures, reduce downtime, and optimize maintenance, improving equipment life and safety
AI helps mining companies predict failures, enhance safety, and optimize efficiency, improving ROI by leveraging data-driven insights and reducing costs
AI-based systems predict energy consumption using data on weather, consumption, and seasonality to reduce operational costs and disruptions
AI predicts weather-related outages, improving restoration times and enhancing customer and regulatory satisfaction for utility providers
AI anticipates renewable energy efficiency, predicts demand, and boosts operational efficiency by optimizing energy usage and selling stockpiled energy
AI-powered defect detection identifies faults early, reducing losses, extending asset lifecycle, and ensuring employee safety while protecting investments and the environment
IoT and visual inspection identify defects, reduce costs, and improve efficiency by eliminating faulty items before production continues
AI combines IIoT and real-time data to ensure safety and compliance, detecting leaks and environmental concerns in tightly regulated industries
AI optimizes production, energy savings, and quality in competitive markets using digital twins for process improvements and performance assessment
AI and analytics forecast raw material needs, streamline supply chains, prevent overstocking, estimate pricing, and enhance just-in-time production for chemical processes
Client is a leading Fortune 500 company in chemical business. It has a significant presence in specialty chemicals value chain through offerings in epoxy, food phosphates, sulphites and water treatment chemicals.
Client is a state owned Indian hydel power generation company operating three power plants with generation capacity between 30 MW to 240 MW in India. These power plants have been operational since decades using equipment’s from different manufacturers.
Client is a multinational metals and mining corporation, producing iron ore, copper, diamonds, gold and uranium.
Client is a leading Fortune 500 company in chemical business. It has a significant presence in specialty chemicals value chain through offerings in epoxy, food phosphates, sulphites and water treatment chemicals.
Client is a state owned Indian hydel power generation company operating three power plants with generation capacity between 30 MW to 240 MW in India. These power plants have been operational since decades using equipment’s from different manufacturers.
Client is a multinational metals and mining corporation, producing iron ore, copper, diamonds, gold and uranium.