In the wake of the first (1973) and the second (1979) global oil crises and growing environmental concerns, the world stands at a critical crossroads. As our population swells and economies expand, so too does our insatiable appetite for energy. This surge in demand, particularly in industrial sectors, is placing unprecedented strain on our finite petrochemical resources. These energy-intensive giants, while essential for countless manufacturing processes, have become the focal point in our quest for sustainability.
The imperative is clear: we must revolutionize how we approach energy consumption in these industrial behemoths. As we embark on this journey, one solution stands out for its transformative potential: leveraging data to optimize fuel efficiency in industrial furnaces.
The Current Landscape:
Industrial furnaces, the workhorses of manufacturing, metallurgy, and materials processing, have long been known for their voracious appetite for fuel. Traditional approaches to fuel efficiency in furnaces have relied on periodic adjustments based on general guidelines and operator experience. While these methods have yielded improvements, they pale in comparison to the potential offered by data-driven strategies. With global energy prices fluctuating and environmental regulations tightening, the pressure to optimize fuel usage has never been more intense.
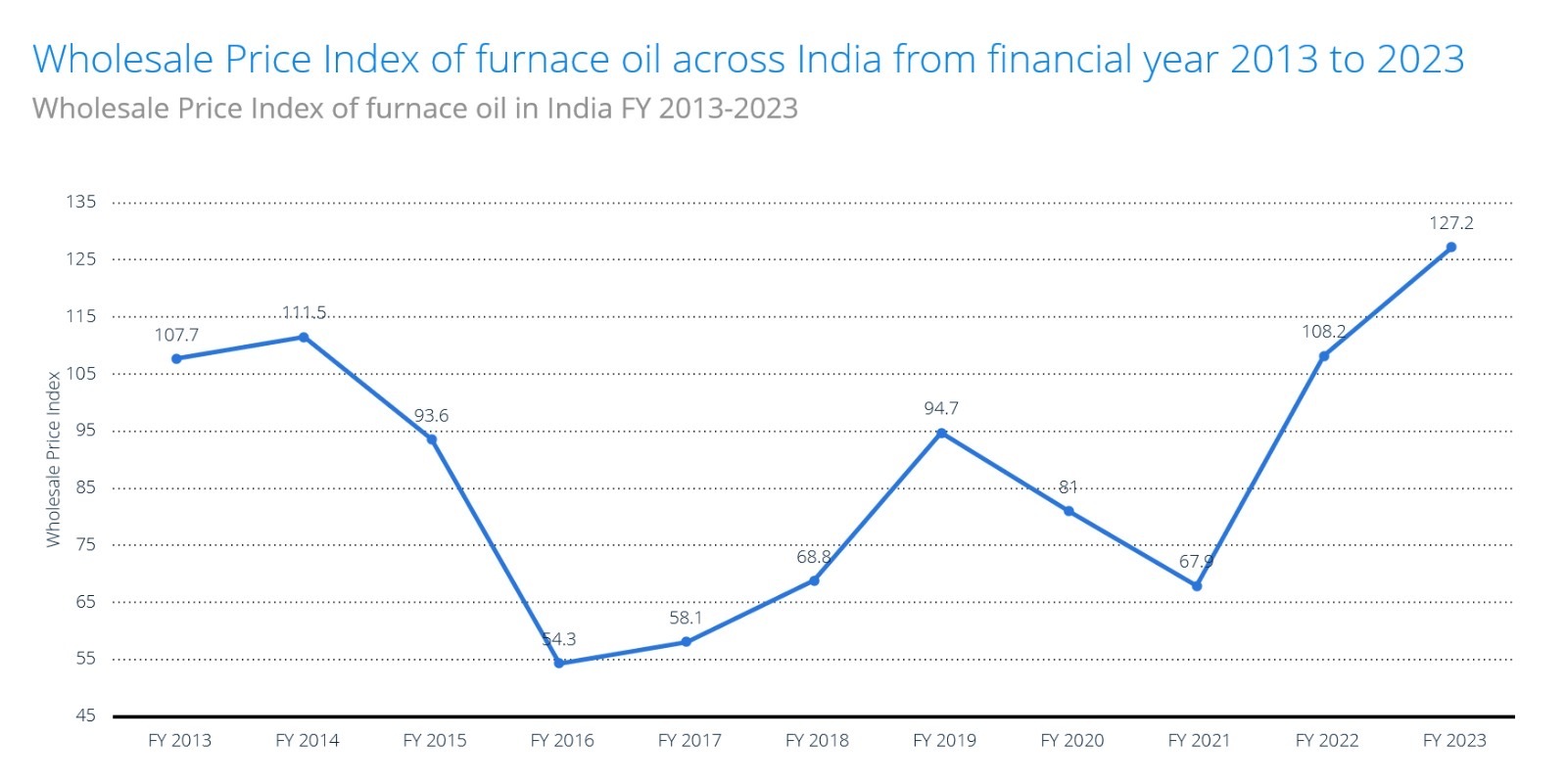
This data on the Wholesale Price Index of furnace oil in India from 2013 to 2023 highlights the volatile nature of fuel costs for industrial furnaces, underscoring the critical importance of data-driven optimization strategies. This volatility emphasizes why leveraging data to reduce fuel consumption is crucial for maintaining profitability and competitiveness.
By implementing advanced data analytics, real-time monitoring, and predictive modeling, companies can adapt quickly to price changes, optimize fuel usage, and mitigate the impact of market volatility.
The global oil consumption data from 2010 to 2022 reveals a shifting landscape that underscores the urgency of our topic.
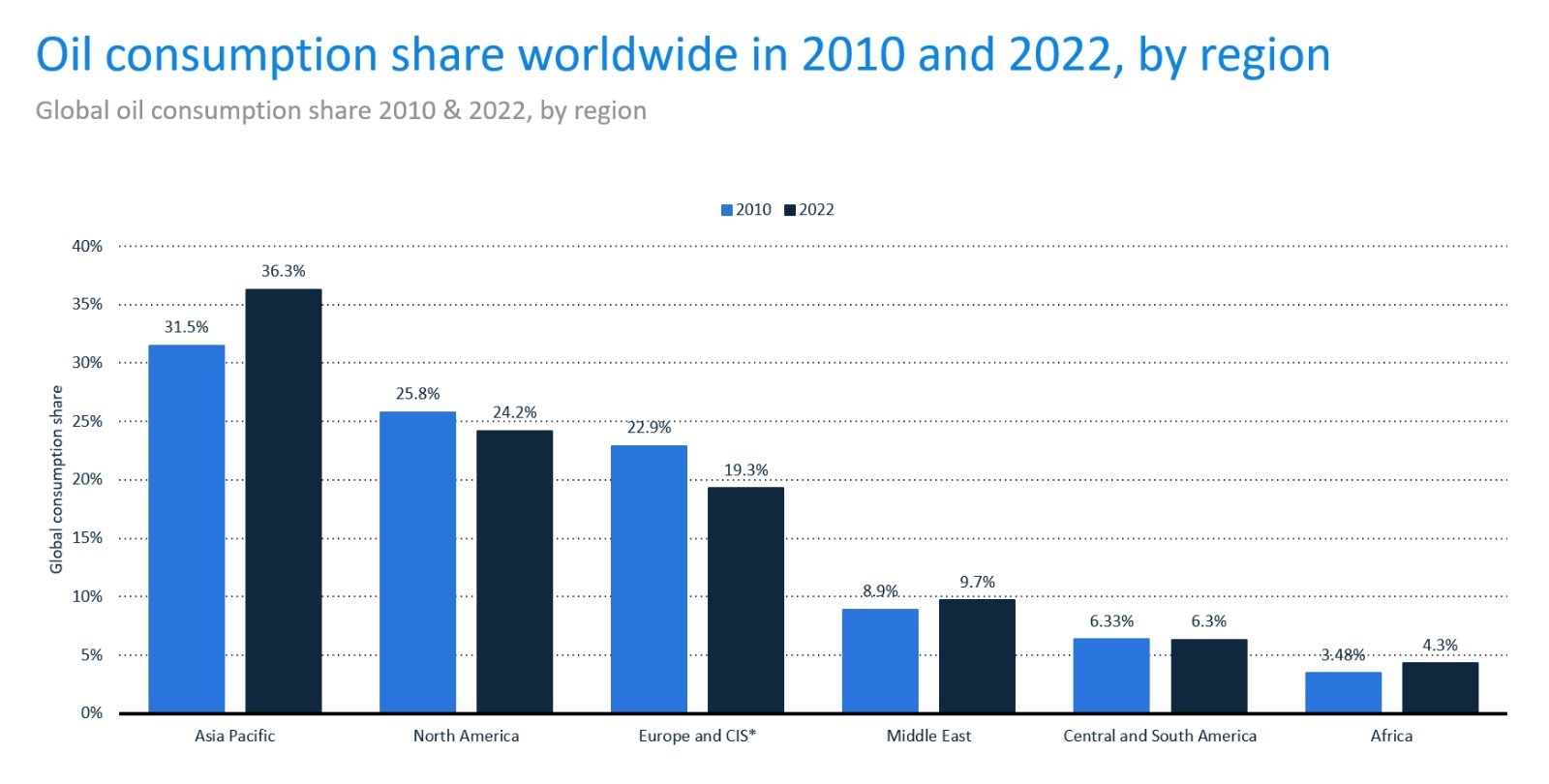
While Asia Pacific’s share surged from 31.5% to 36.3%, reflecting rapid industrialization. This divergence highlights the critical need for data-driven fuel optimization in industrial furnaces worldwide. The data not only illustrates the challenge of balancing industrial growth with resource conservation but also points to the potential for significant impact through innovative approaches to fuel consumption reduction, especially in energy-intensive processes like industrial furnace operations.
The Data-Driven Approach:
In the realm of industrial furnace optimization, the data-driven approach represents a paradigm shift from traditional heuristic methods to a sophisticated, multifaceted strategy. This approach leverages advanced technologies and methodologies to create a closed-loop system of continuous improvement. Let’s delve into the three pillars of this revolutionary approach:
1. Multi-Modal Data Acquisition and Integration
The foundation of our data-driven strategy lies in the comprehensive capture of heterogeneous data streams. This goes beyond basic temperature and fuel flow measurements, encompassing:
- High-frequency thermal imaging for real-time heat distribution analysis
- Spectroscopic flue gas analysis for combustion efficiency monitoring
- Acoustic sensors for flame stability assessment, material composition sensors for feed quality variation detection
- Environmental sensors for ambient condition impact analysis
The key innovation here is the integration of these diverse data streams into a unified, time-synchronized dataset.
2. Advanced Analysis and Predictive Models
With a rich dataset in hand, sophisticated analysis techniques can uncover valuable insights:
- A combination of different computer models can understand both simple and complex relationships in how the furnace behaves.
- Patterns over time can be analyzed to forecast future furnace performance accurately.
- Systems can be implemented to quickly spot unusual behavior that might indicate inefficiencies or potential equipment problems.
- Virtual copies of furnaces can be created that combine scientific principles with real-world data, allowing for safe and efficient scenario testing.
These models don’t just make predictions; they can provide clear explanations that help operators understand and trust the results, supporting ongoing improvements.
3. Self-Improving Control Systems
The final piece of this approach is a control system that continuously adapts to changing conditions:
- Advanced control algorithms can balance multiple goals like fuel efficiency, product quality, and emissions, while staying within safe operating limits.
- Learning systems can be implemented to figure out the best control strategies over long periods of operation.
- Smart optimization techniques can efficiently handle processes with many variables, especially useful when dealing with varying raw material qualities.
- Secure methods can be used to share insights across multiple furnaces or even different plants, while keeping each facility’s data private.
This approach transcends traditional efficiency measures, paving the way for autonomous, hyper-efficient furnace operations that were previously thought unattainable.
By embracing this data-driven paradigm, industries can expect not just incremental improvements, but transformative changes in their energy consumption patterns.
The Benefits Beyond Fuel Savings:
While optimizing fuel consumption in industrial furnaces is our primary objective, the data-driven approach catalyzes a transformation that extends far beyond energy savings. This strategy is reshaping the industrial landscape, offering a multitude of benefits that propel businesses into a new era of operational excellence.
1. Unprecedented Product Quality Consistency:
Furnace optimization significantly enhances product quality through three key mechanisms. Advanced spatial temperature control ensures thermal uniformity, reducing gradients and improving material consistency. Real-time atmospheric adjustments, guided by spectroscopic analysis, optimize chemical reactions and minimize defects. Adaptive machine learning models compensate for raw material variations, maintaining consistent output quality across batches. These integrated approaches lead to fewer rejections, higher yields, and superior product reliability, offering manufacturers a substantial competitive advantage in precision-dependent industries.
2. Operational Capacity Amplification:
Data-driven approaches substantially boost furnace productivity through three primary avenues. Predictive heat transfer modeling optimizes heating cycles, accelerating throughput without new capital investments. Advanced maintenance algorithms, utilizing acoustic and vibration data, predict and prevent failures, minimizing unplanned downtime and enhancing overall equipment effectiveness. AI-powered scheduling optimizes furnace loading patterns, maximizing energy efficiency and effective capacity. Together, these innovations drive significant improvements in productivity, allowing manufacturers to extract more value from existing assets while reducing operational disruptions.
3. Proactive Maintenance Ecosystem
Advanced anomaly detection models accurately predict equipment failures, enabling proactive maintenance. Optimized operating conditions extend the life of critical components, particularly refractory linings. Risk-based maintenance scheduling, guided by digital twin simulations, reduces costs while enhancing equipment reliability. This comprehensive strategy minimizes unexpected downtime, extends operational life, and improves return on investment, ultimately reducing long-term capital expenditure needs for industrial furnace operators.
4. Financial Performance Amplification
It transforms cost structures, reduces operational expenses, and boosts return on assets through improved equipment effectiveness. Enhanced demand forecasting and production flexibility enable rapid market adaptation, potentially increasing market share. These improvements drive profitability, competitive advantage, and long-term financial sustainability for manufacturers adopting advanced optimization strategies.
The journey towards data-driven furnace optimization transcends mere fuel consumption reduction—it catalyzes a comprehensive transformation of industrial operations. By embracing this holistic approach, companies position themselves at the forefront of the fourth industrial revolution, ready to navigate the complexities of a rapidly evolving global market with agility, efficiency, and innovation.
The future belongs to those who can harness the power of data to not just optimize individual processes, but to reimagine the very fabric of industrial operations. As we stand on the brink of this new era, the question is not whether to embrace this transformation, but how quickly we can implement it to stay ahead in an increasingly competitive global landscape.
Overcoming Implementation Challenges:
While the benefits of data-driven furnace optimization are clear, implementation is not without its challenges. Common hurdles include:
- Initial investment costs for sensors and analytics platforms
- Resistance to change from operators accustomed to traditional methods
- Integration with existing systems and processes
- Data security and privacy concerns
Successful implementation requires a holistic approach that addresses these challenges head-on. This often involves:
- Phased implementation to demonstrate value and build buy-in
- Comprehensive training programs for operators and managers
- Collaboration with IT departments to ensure seamless integration and data security
- Partnership with experienced solution providers who understand both the technical and human aspects of digital transformation
The Future of Furnace Efficiency:
The future of industrial furnace optimization is set to revolutionize manufacturing through cutting-edge technologies. Edge computing will enable instant, data-driven adjustments, while AI-driven design will create ultra-efficient furnace configurations. Advanced materials, developed with data insights, will enhance durability and performance. Blockchain technology will allow furnaces to dynamically participate in energy markets, optimizing fuel use based on real-time prices. This convergence of innovations promises to dramatically reduce costs, minimize environmental impact, and create new competitive advantages. As these technologies mature, they will redefine efficiency standards and open unprecedented opportunities for innovation in thermal processing industries.
The Road Ahead:
The journey towards fully optimized, data-driven industrial furnaces is not just about technology—it’s about a fundamental shift in how we approach industrial processes. It requires a mindset that values continuous improvement, embraces data-driven decision-making, and recognizes the interconnectedness of efficiency, quality, and sustainability.
For companies willing to embark on this journey, the rewards are substantial. Beyond the immediate benefits of reduced fuel consumption and lower operating costs, data-driven optimization positions businesses at the forefront of the industry 4.0 revolution. It creates a foundation for ongoing innovation and adaptation in a rapidly changing industrial landscape.
Key Takeaways:
- Paradigm Shift in Optimization: The future of industrial furnace efficiency lies not in incremental improvements, but in a holistic, data-driven reimagining of the entire process. This approach transcends traditional methods, ushering in an era of smart, adaptive manufacturing.
- Integrated Data Ecosystem: Success hinges on creating a comprehensive, multi-modal data acquisition system that captures every aspect of furnace operation. The integration of diverse data streams provides unprecedented insights into the complex dynamics of industrial processes.
- AI as a Cornerstone of Efficiency: Advanced analytics and machine learning models are not just tools, but integral components of the modern furnace operation. These technologies enable predictive capabilities and continuous optimization that surpass human cognitive limitations.
- Beyond Fuel Savings: While reducing fuel consumption is a primary goal, the benefits of data-driven optimization cascade throughout the entire operation, impacting product quality, operational capacity, maintenance strategies, and environmental performance.