The Fragmented Landscape of Industrial Operations
In the intricate world of industrial operations, departments such as manufacturing, maintenance, logistics, and energy management often function in isolation. Each department utilizes its own systems, collects its own data, and makes decisions based on its unique perspective. This siloed approach can lead to inefficiencies, misaligned objectives, and missed opportunities for optimization.
The advent of Artificial Intelligence (AI) offers a transformative solution. By integrating AI across the entire industrial value chain, organizations can break down these silos, enabling seamless communication and collaboration between departments. This integration not only enhances operational efficiency but also drives innovation and competitiveness in an increasingly complex market.
The Cost of Siloed Operations
Operating in silos can have significant repercussions:
- Inefficiencies: Without integrated systems, processes can become redundant, andresources may be underutilized.
- Delayed Decision-Making: Lack of real-time data sharing hampers swiftdecision-making, leading to slower response times.
- Increased Costs: Isolated operations can result in higher maintenance costs, inventory mismanagement, and energy wastage.
- Reduced Agility: Organizations may struggle to adapt to market changes or disruptionsdue to fragmented information flows.
A study by McKinsey highlights that companies integrating digital technologies across their operations can reduce costs by up to 20% and increase efficiency by 30% (Source:Reuters)
AI: The Catalyst for Integration
In traditional industrial environments, operations often exist in silos—maintenance teams operate independently of logistics, quality assurance is detached from energy management, and production functions on its own timeline. This fragmentation leads to inefficiencies, misaligned decision-making, and suboptimal use of resources.
Predictive Maintenance: Preempting Failure Before It Happens
AI algorithms, particularly those leveraging machine learning and time-series analysis, are transforming maintenance from a reactive to a predictive function. By analyzing real-time data from IoT sensors (vibration, temperature, acoustic, etc.), these systems detect early signs of equipment degradation and predict potential breakdowns.
- According to McKinsey, predictive maintenance can reduce equipment downtime by up to 70%.
- Maintenance costs are slashed by nearly 25%, and inspection efforts are minimized by 50%. (Source)
- A Deloitte study found that predictive models could increase asset lifespan by 20–40%, delivering a direct impact on capital expenditure.
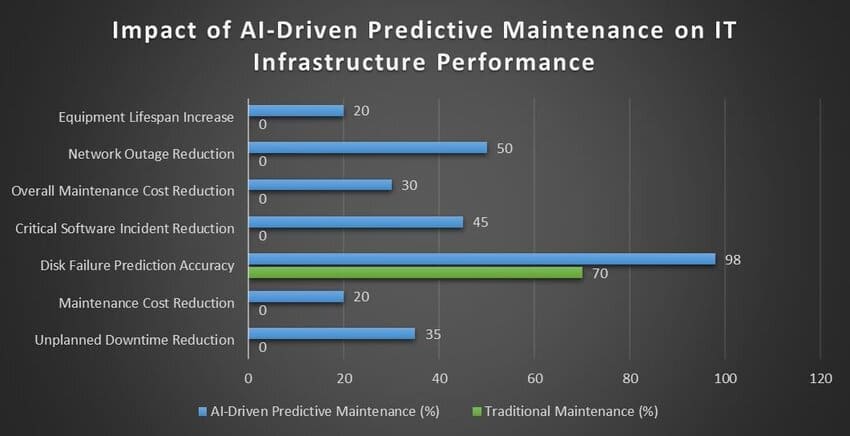
(Source)
Quality Control: Ensuring Consistency with Machine Vision
Quality control in industrial environments is often a manual and error-prone process. AI-enabled computer vision systems now allow real-time inspection across production lines, identifying micro-defects invisible to the human eye.
These systems use convolutional neural networks (CNNs) trained on thousands of defect types to detect anomalies in shape, texture, alignment, or material integrity.
- A Capgemini report shows AI-powered vision systems have improved defect detection rates by 90%+.
- Scrap rates have dropped by 30%, and rework effort has been reduced significantly.
- Enterprises using these systems report an increase in first-time-right production from 85% to over 95%. (Source)
Supply Chain Optimization: End-to-End Intelligence
AI brings unprecedented visibility and precision to the supply chain. By processing historical data, weather conditions, demand signals, and supplier performance, AI systems generate highly accurate demand forecasts, optimize inventory levels, and streamline logistics operations.
Large language models (LLMs) and reinforcement learning are even being deployed for scenario planning, allowing businesses to simulate disruptions and optimize recovery strategies.
- Mckinsey reports that AI in supply chain operations reduces forecasting errors by 20–50%.
- Inventory carrying costs can drop by up to 30%.
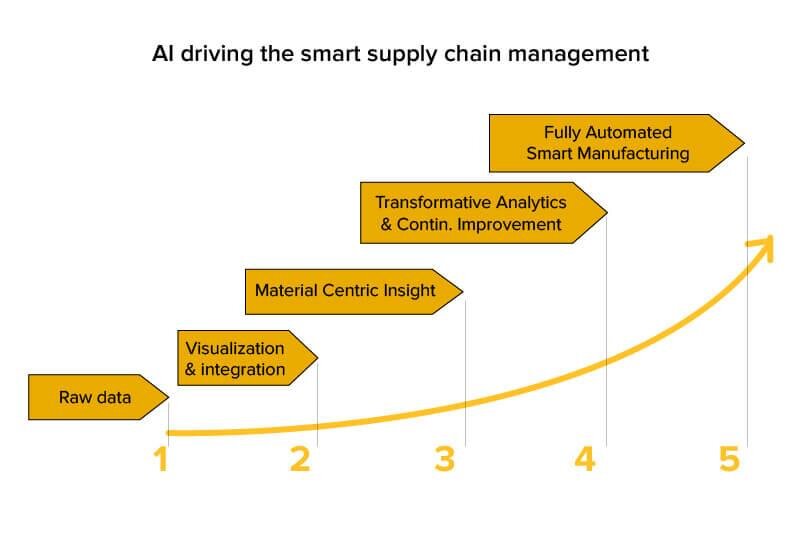
(Source)
Energy Management: Smart Consumption, Sustainable Operations
Energy usage is often one of the largest controllable expenses in industrial operations. AI-powered energy management systems continuously monitor usage patterns, detect inefficiencies, and optimize power consumption to align with operational demands and sustainability targets.
AI also supports demand response strategies, predicting peak load times and adjusting machinery operation accordingly to reduce strain and cost.
- The International Energy Agency (IEA) states AI-enabled energy optimization can cut industrial energy use by 10–20%.
- Companies integrating AI with HVAC and production machinery have seen energy cost reductions of up to 25%. (Source)

Valiance Solution’s Role in AI-Driven Integration
Valiance offers a comprehensive AI platform designed to unify industrial operations:
- Data Integration: The platform seamlessly ingests data from various sources, including ERP, SCADA, and IoT systems, providing a centralized view of operations.
- Advanced Analytics: Utilizing machine learning, the platform analyzes data to uncover patterns, predict outcomes, and recommend actions.
- User-Friendly Dashboards: Customizable dashboards offer real-time insights, enabling stakeholders to make informed decisions quickly.
- Scalability and Interoperability: Designed to scale with business growth, the platform integrates effortlessly with existing systems, ensuring minimal disruption.
By providing end-to-end visibility, Valiance empowers organizations to transition from reactive to proactive operations, fostering a culture of continuous improvement.
Real-World Impact: Powering Efficiency in Energy
Valiance partnered with a state-run hydel power company to unify operations across plants using a cloud-based IoT and AI platform. The result? Centralized monitoring, predictive maintenance, and improved energy efficiency.
Read the full case study: Click here
Strategic Benefits of AI Integration
Integrating AI across the industrial value chain offers numerous strategic advantages:
- Enhanced Decision-Making: Real-time data analytics empower stakeholders to make informed decisions swiftly.
- Operational Efficiency: Streamlined processes and predictive maintenance reduce downtime and increase productivity.
- Cost Savings: Optimized inventory management, energy usage, and maintenance schedules lead to significant cost reductions.
- Sustainability: AI-driven energy management supports environmental goals and regulatory compliance.
- Competitive Advantage: Integrated operations enable organizations to respond agilely to market changes and customer demands.
A Mckinsey report indicates that companies implementing AI in their operations can see a 20-30% increase in productivity and a 15-20% reduction in costs.
Conclusion: Embracing the Future of Integrated Operations
The transition from siloed operations to an integrated, AI-driven industrial value chain is not merely a technological upgrade—it is a strategic imperative. By breaking down departmental barriers and fostering collaboration through AI, organizations can unlock unprecedented levels of efficiency, innovation, and competitiveness.
Valiance stands at the forefront of this transformation, offering solutions that not only integrate operations but also pave the way for a smarter, more sustainable industrial future.